جدول المحتويات
Understand Laser Cutting Technology
A Detailed Overview Of Laser Cutting Technology
This guide is tailored to engineers, manufacturers, and business people who are researching laser-cutting alternatives. It addresses laser cutting technology, its corresponding benefits, applications, and emerging technology.
1. What is Laser Cutting?
A focused light beam cuts various materials with high accuracy, in a more efficient manner than other methods; examples of materials include plastics, wood, textiles, and metals.
- Special optics are used to focus a powerful laser onto the surface of the material which is to be cut.
- The laser light beam is usually narrowed to about 0.001 inches (0.025 mm) in diameter and contains laser energy which will either melt, burn, or vaporize depending on the interaction at the contact point.
Compared to traditional machines, modern machines have a higher capability of executing complex and sophisticated shapes alongside intricate designs that were previously thought of as impossible with traditional equipment. During the operation, a jet of gas, typically nitrogen or oxygen is used to blow the molten material while maintaining the clean edges and avoiding contamination of the cutting area.
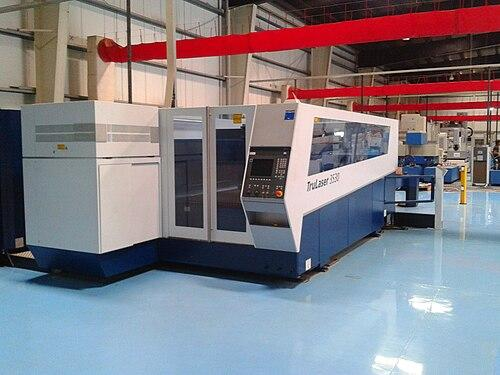
2. Principles of Laser Cutting
Electricity is used to focus light into a light beam. Depending on the type used, the laser is set to focus on specific wavelengths. The light is transformed into a highly concentrated light that can deliver a great deal of thermal energy, enough to melt, burn, or vaporize the material underneath it. The power density that can be achieved in this case may reach several megawatts per square centimeter. This makes it possible to work with materials from thin sheets to plates of thick metals.
- This lens captures the energy and concentrates it to a spot smaller than or equal to 0.32 mm in diameter, resulting in exceptional power at the cutting point.
- This focus allows the laser to cut at a rate of several meters per minute, depending on the material type and thickness.
A gas, such as oxygen, nitrogen, or even compressed air, is introduced into the cutting head at 1 to 20 bar pressure. This gas serves many vital purposes: blowing molten material out of the cut area, preventing it from reattaching, protecting the lens from overheating material, causing potential damage, and sometimes participating in the cutting action via thermal exothermic reactions. The type of gas used has a profound impact on cutting quality and speed – for example, in the case of cutting mild steel, oxygen enhances the rate due to exothermic reactions. Nitrogen, however, produces a clean, oxide-free cut on stainless steel and aluminum.
- Sophisticated CNC (Computer Numerical Control) technology controls the number of axes programmed on the cutting path. Each of the motion axes runs at microsecond precision.
- Such a level of digital control facilitates unparalleled accuracy, in this case, within ±0.1 millimeters of the material: unmatched repeatability during numerous cuts and intricate features, as well as cutting process constancy throughout multi-faceted cutting processes.
The most recent designs of CNC systems integrate seamlessly with CAD/CAM systems, enabling the crafting of automated toolpaths, monitoring of the task during the process, and controlling vital parameters such as power, speed, and assist gas pressure. Such accuracy provides the ability to perform intricate cuts without losing quality uniformity across mass production.
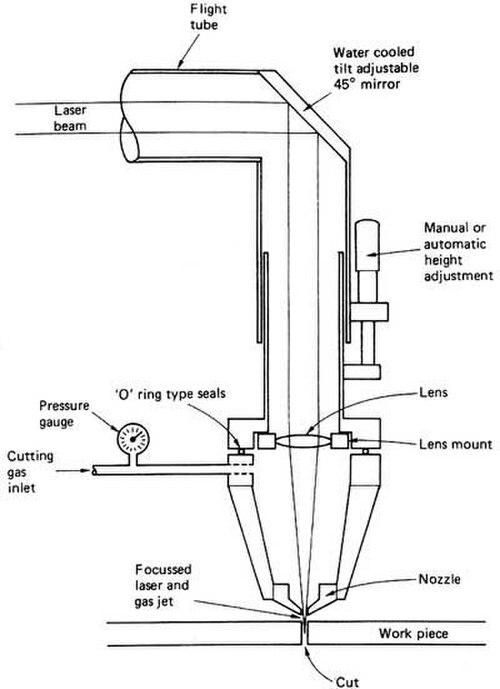
3. Illustrating the Benefits and Drawbacks of Laser Cutting Technology
المزايا
Unlike other common methods, laser cutting provides an unequaled level of precision and accuracy.
- The capability of applying a focused beam for cutting results in the production of very clean edges and minor deformation of the material, which is ideal for intricate designs and tight tolerances.
- Laser cutting technology shows great versatility as it can work with materials composed of metals, plastics, wood, and even textiles. This flexibility makes it a valuable tool in multiple industry sectors and various applications.
- The technology slashes the time needed for production, reduces material waste, and virtually eliminates the need for retooling between different jobs.
- With the modern systems of laser cutting, automation features lead to a decrease in labor costs and an increase in output. A large number of the systems available today can run for long periods with little operator attention.
- The fact that there is no contact with the cutting tool is a major asset. This eliminates tool wear phenomena associated with traditional cutting methods, consistent production quality is maintained throughout production cycles, and maintenance requirements are much lower.
Disadvantages
While laser cutting provides precision and accuracy, there are disadvantages to the method.
- Significant capital investment is required for the machinery, software, and other building infrastructure changes needed for quality systems.
- Regarding material restrictions, the flexibility of laser technology is somewhat limited. Certain types of lasers are needed for highly reflective metals such as brass and copper, and some materials may release toxic gases when cut.
- The energy costs of operating lasers remain quite high. The cost of running the equipment, especially when cutting thicker materials, is high due to the power demands associated with cutting operations.
- There is a requirement for specialized knowledge regarding the operation and upkeep of laser cutting systems. Sophisticated technicians need to be well-versed in the mechanical and software control components.
- Sensitive applications may be affected by the heat-affected zones. The laser’s thermal cutting mechanism can change the structural properties of the material at the boundaries close to the cut.
4. Introduction of Two New Types of Laser Cutting Machines
a.Laser Cutting Machine (CO2)
CO2 laser cutting machines are most effective when working on non-metallic materials like wood, plastics, acrylic, textiles, and even paper. CO2 lasers are gas molecular lasers and employ supplementary gases like nitrogen, xenon, helium, and hydrogen, which increase the thermal stability and efficiency of the beam.
- CO2 laser machines operate at a frequency of 10.6 micrometers, meaning organic materials will readily absorb the lasers.
- Because of this, CO2 laser machines have proven effective when cutting and engraving non-metals with intricate details.
- When the laser is focused appropriately, it produces a wavelength that minimizes distortion, enabling cutting with fine detail.
- Advanced CO2 systems use circularly polarized beams that greatly reduce harmful reflections and increase cutting efficiency for metals like aluminum and brass, making these systems effective for cutting reflective metals.
- Tapering the thickness of the material results in an increase in cutting speed, up to 30 meters per minute. The beam quality ensures the edge finishes are smooth, making secondary operations like polishing obsolete.
- The more advanced systems come equipped with automatic capacitance sensing height followers, which enable the laser head to retain a constant distance to the surface of the material being cut, ensuring a consistent focus and cut quality on uneven surfaces.
Today’s CO2 laser systems come with intuitive controls and a broad database of materials. These functions ease the operation of users while maintaining proper cutting settings for different materials and their thicknesses. The Control systems, like the Ruby® laser software, permit users to work from design to a finished product and incorporate functionalities like auto-focusing, red light marking, and integrated system diagnostics, which further enhance precision.
The introduction of high-resolution cameras used for positioning, modular maintenance-free dockable laser tubes, advanced cooling systems that improve energy efficiency while maintaining cooling performance, and other innovations of the system are recent. All these developments are in line with the rest of the manufacturing industry shifts towards sustainable manufacturing, the fourth industrial revolution, and the industrial Internet of Things.
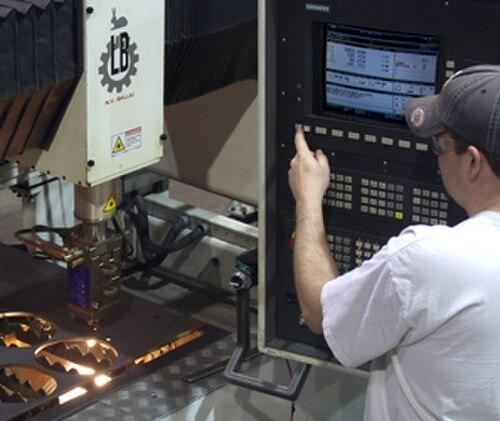
b.Laser Cutting Machine (Wide Format)
Wide format laser cutting machines are specially designed for maximum precision.
- Because of the advanced work areas, wide format laser cutting machines meet the industry standards for mass production.
- The cutting envelope typically spans from 1.5 x 3 meters to enormous 4 x 20 meter platforms, commanding a shift of standard industrial sheet sizes.
- From foils to 25mm steel plates, wide format machines are able to handle all ranges of material thicknesses.
Automotive, heavy equipment fabrication, and aerospace are just some of the manufacturing sectors which utilize wide format machines because of their versatility.
The design usually includes “flying optics,” where the stationary material is cut by a moving head.
- This configuration enables quick processing of large sheets while sustaining a consistent beam quality throughout the entire cutting area.
- The vertical lifting gantry systems are equipped with linear motors and precision rails that can achieve acceleration rates up to 3G, with positioning accuracy of ±0.05 mm.
- This design removes the problem of moving bulky materials during cutting, which in turn lessens mechanical stress on components and prolongs the service life of the machine.
- New systems come with rigid bridges that greatly reduce cutting vibration, thus guaranteeing the dimensional accuracy all over the working surface at multi-axis high-speed cutting.
- With the use of sophisticated tower storage systems, sheets can be delivered directly to the cutting bed after automatically selecting and delivering the required sheet.
These storage systems can store up to 30 tons of raw materials.
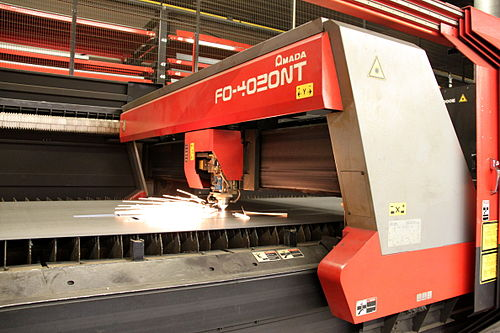
5. Application Field of Laser Cutting
Laser cutting machines have been adopted in many industries:
- Numerous parts of the automobile, both aesthetic and structural, are manufactured in bulk and integrated into various models and makes of vehicles. All of them place heavy reliance on precision laser cutting for level and intricate detailing, such as on dashboards.
- This technology is routinely used in aerospace manufacturing for complex aircraft engine parts, fuselage components, and interior parts.
- The electronics sector relies on precision laser cutting for circuit boards and components housing. Micro precision laser cutting allows for the manufacture of smaller and more complex devices with intricate internal design.
- Laser cutting is employed extensively in the manufacture of surgical instruments and implantable devices within the medical device industry. Its high relevance to biocompatible materials stems from the ability to create clean cuts with a minimal heat-affected zone.
- Lasers provide endless possibilities for fashion and textile design, which is the reason they have gained so much popularity in these two industries.
- Designers employ the technology in question to create designs and embellishments with cutting methods far too advanced to be achieved using more traditional means.
- Custom metal facades, decorative panels, and pre-cut building components serve as some architectural use cases. Complex architectural elements are automatically aligned with the rest of the components due to the precision and repetitiveness of the function from laser cutting.
- A display and sign-making business would make use of laser cutting because of its versatility with materials. Intricate displays are possible because the technology produces precise edges.
- Because laser cutting allows for custom patterns, the furniture manufacturing industry can use it for decorative inlays and intricate joint designs maximizing the value of the products.
- Casing and internal components of consumer electronics are increasingly adopting the use of laser cutting. With the help of laser cutting, manufacturers are able to accurately make consistent cuts for ports, buttons, and other parts without obstructing the quality.
Each industry, no matter what it is, benefits from diversity due to precision, speed, and compatibility with materials.
6. The Future Development Trend of Laser Cutting Technology
There are exciting developments coming in laser cutting, including:
- Ultrafast laser systems. These systems utilize femtosecond and picosecond pulses to achieve “cold cutting,” which means no heat-affected zone will be present.
- Operations for laser cutting will go through a major change with the integration of AI and machine learning.
- These technologies support real-time process changes, predictive maintenance, and automated defect identification.
- Hybrid laser technology advances are improving the processing of highly reflective materials such as gold, copper, and brass. As an example, green lasers have a shorter wavelength providing better absorption.
- Next-generation laser systems are designed to be more energy efficient without sacrificing cutting performance.
- Certain applications benefit from the mechanical removal of the cutting head and are able to achieve greatly increased processing speeds. These applications are broadened by remote laser cutting that uses scanner systems instead of traditional cutting heads.
- Complementary processes are laser cutting that utilize a form of hybrid manufacturing systems. These integrated solutions incorporate forming, welding, or 3D printing within one machine platform.
- Monitoring and operating systems that use the cloud allow management of laser cutting equipment from different locations. They enable real-time tracking of the production, optimization of resources, and support of new collaborative frameworks for manufacturing.
- New specialized laser sources allow more advanced material with previously difficult materials like carbon fiber composites, ceramics, and semiconductor materials. Specialized laser sources continue to expand.
- Microprocessing capabilities are advancing to meet demands from the electronics and medical industries. The latest generation laser systems achieve microns for feature sizes with unmatched precision for previously impossible tasks.
Looking forward, the integration of AI, new automation technologies, and modern laser sources will evolve manufacturing even further with improved precision, flexibility, and eco-friendliness while decreasing the need for human input automation.
7.Summary
Across industries, laser cutting’s focused light energy fundamentals are the principle and core for use in aerospace, medical, and even consumer products. Each day, lasers are offered for more and more use cases and to expand their capabilities.
CO2 systems have a wide array of applicability and excel at non-peripheral processing at great detail, and wide-format machines excel in providing mark-level efficiency at industrial scale production. These systems, as with all that make use of laser cutting, offer unrivaled benefits of speed, precision, and versatility at reduced waste.
The promising future of the technology is a result of incorporating AI along with sustainable practices and advanced materials processing capabilities. Businesses that are always looking for an upper hand with unmatched precision and efficiency are set to make use of laser cutting and will strengthen their foundation in core manufacturing technology.
Understanding these fundamentals—focusing on laser cutting—can transform production capabilities, unlock new market opportunities, and provide significant competitive advantages in today’s ever-demanding manufacturing landscape.