Laser marking is an advanced marking technique that uses focused laser engraving technology to carve characters, patterns, and logos on the surface of an object. Compared to traditional printing methods, laser marking offers superior quality, high consistency, durability, efficiency, cost savings, and reliability. It has become widely used in the PCB (Printed Circuit Board) industry.
Market Demand Driven by Technological Advancements
With the booming development of the IT industry, products like smartphones and wearable electronics continue to become thinner and smaller. As consumer demands for electronic products grow, the production of PCBs must also meet increasingly stringent quality standards. To achieve quality control during PCB production, marking characters, barcodes, QR codes, and other information for traceability has become an industry trend.
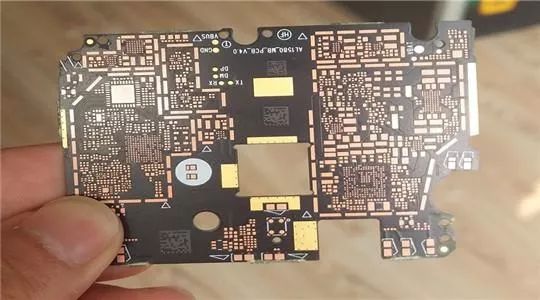
Why Traditional Printing Is No Longer Enough
Traditional printing methods are no longer able to meet the evolving demands of the market due to several disadvantages:
- Poor Durability: The durability here refers to the fact that the ink on the PCB surface can wear off during use, causing blurriness, fading, and other issues.
- Aesthetic Requirements: Metal surface printing often looks lower-end. This is unsuitable for products that require a high-quality appearance, such as commemorative badges, metal business cards, elegant promotional plaques, or crafts.
- Environmental and Health Risks: Traditional printing processes involve the use of toxic chemicals such as organic solvents and heavy metals. These substances can be harmful to workers and contribute to environmental pollution as volatile chemicals evaporate during the drying process.
As the quality of electronic products continues to improve, consumers’ demands for the quality of PCB markings are also rising. Traditional printing technologies, which were once sufficient, are now falling short. Laser marking, on the other hand, addresses these challenges and has become a key trend in the PCB industry.
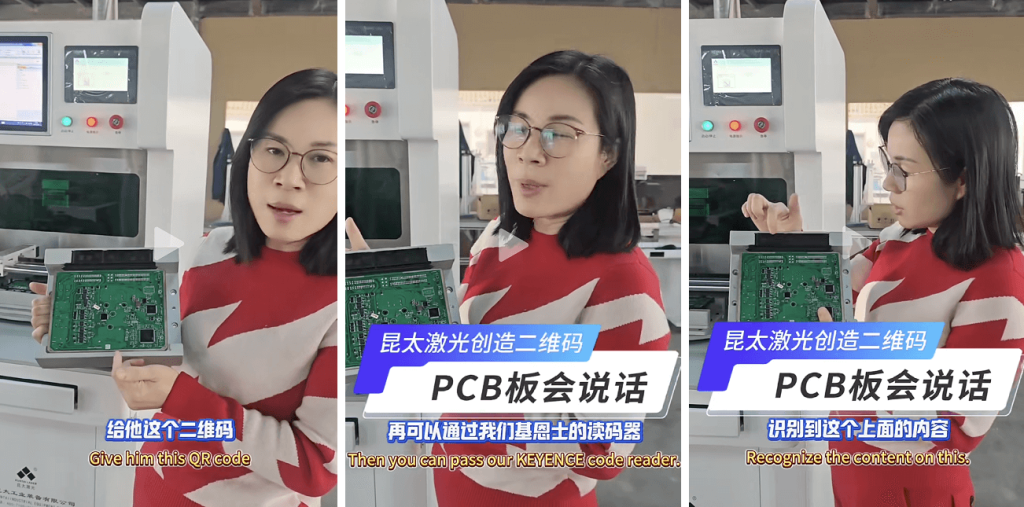
By utilizing laser technology, companies can achieve superior durability, precision, and aesthetic quality—meeting the rising expectations of both manufacturers and consumers.
Advantages of Laser Marking Over Traditional Printing
- Superior Quality & Durability
- Produces clear, aesthetically pleasing markings, including logos, patterns, QR codes, and text.
- The markings are directly engraved onto the material, ensuring exceptional durability.
- High Precision Processing
- Laser beams can be focused to an ultra-fine diameter of just 10μm (for UV lasers), enabling intricate and precise engraving.
- Efficiency & Cost Reduction
- Simple computer-controlled operation; users can set parameters and complete marking in just a few seconds.
- Reduces labor costs and enhances production efficiency.
- Non-Destructive Marking
- Laser marking is a non-contact process, preventing material damage and ensuring high-quality results.
- Wide Material Compatibility & Environmental Benefits
- Suitable for marking a variety of thin metal and non-metal materials.
- A clean, chemical-free process that is safe for both workers and the environment.
- Stable Performance & Long Lifespan
- Advances in laser technology have significantly extended the lifespan of laser equipment, ensuring long-term reliability.
Laser Marking in the PCB Industry
The two most widely used laser marking methods in PCB manufacturing are UV laser marking and CO₂ laser marking. These technologies stand out for their:
✅ Minimal heat impact
✅ High processing precision
✅ Fast marking speed
✅ Excellent marking quality